Titanium
Titanium, a lightweight and corrosion-resistant metal, has gained popularity in various industries due to its exceptional properties. This blog post explores the applications of titanium bolts, fasteners, and washers, highlighting their advantages, manufacturing methods, and the services provided by GY Machining Custom CNC Machining.
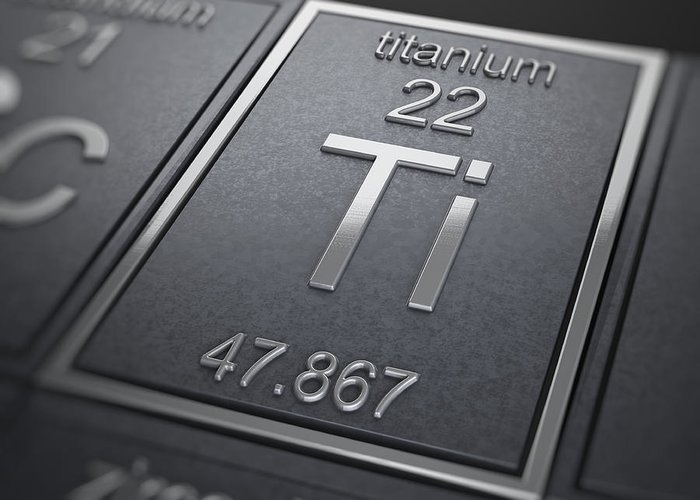

- Titanium Materials: Advantages and Properties
Titanium is a versatile metal known for its exceptional properties and has gained significant popularity in various industries. Some of the key advantages and properties of titanium include:
Superior Strength-to-Weight Ratio
Titanium is renowned for its impressive strength-to-weight ratio, making it an ideal choice for applications where weight reduction is critical. Despite being about half the weight of steel, titanium exhibits remarkable strength, allowing for the design of lighter and more efficient structures.
Excellent Corrosion Resistance
One of titanium’s most remarkable attributes is its exceptional resistance to corrosion. It forms a protective oxide layer on its surface when exposed to oxygen, which makes it highly resistant to corrosive elements such as saltwater, acids, and chemicals. This corrosion resistance makes titanium bolts, fasteners, and washers suitable for applications in harsh environments, including marine and aerospace industries.
High Temperature Resistance
Titanium exhibits excellent heat resistance, with a melting point of approximately 1,670°C (3,038°F). It retains its strength and integrity even at elevated temperatures, making it suitable for applications that require exposure to high heat, such as jet engines, exhaust systems, and industrial equipment.
Biocompatibility and Non-Toxicity
Titanium is biocompatible, meaning it is compatible with the human body and is widely used in medical and dental implants. It exhibits excellent osseointegration properties, allowing implants to bond with surrounding bone tissue effectively. Additionally, titanium is non-toxic, making it a safe choice for medical applications.
Impressive Fatigue Strength
Titanium demonstrates exceptional fatigue strength, enabling it to withstand repeated loading and cyclic stress without experiencing fatigue failure. This property is crucial for applications that require long-term durability, such as aerospace structures, automotive components, and high-performance sports equipment.
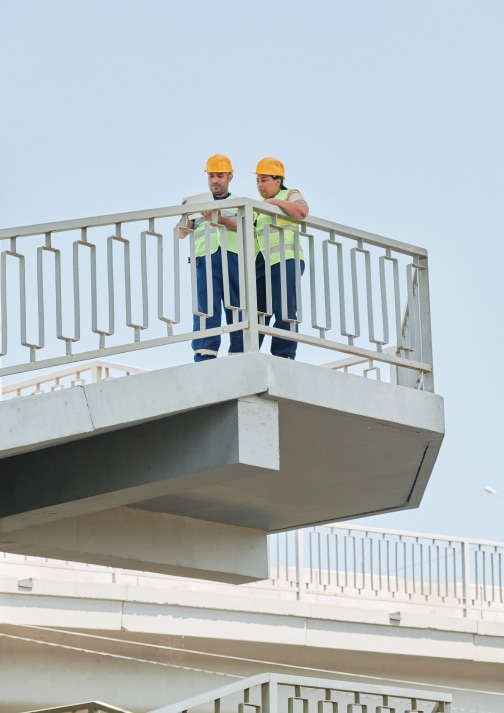
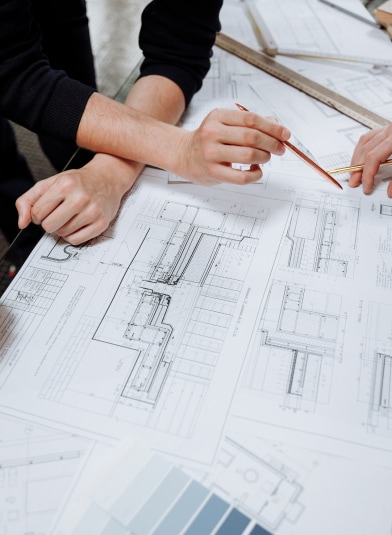
train station renovation (2016-2017)
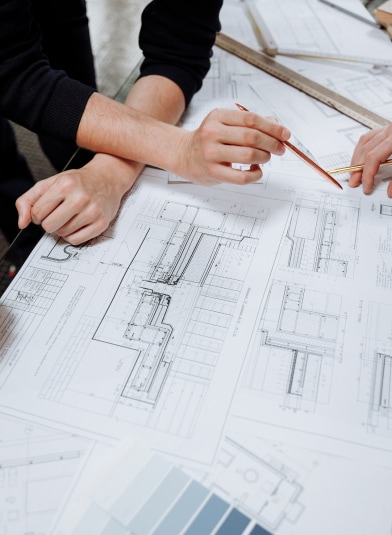
train station renovation (2016-2017)
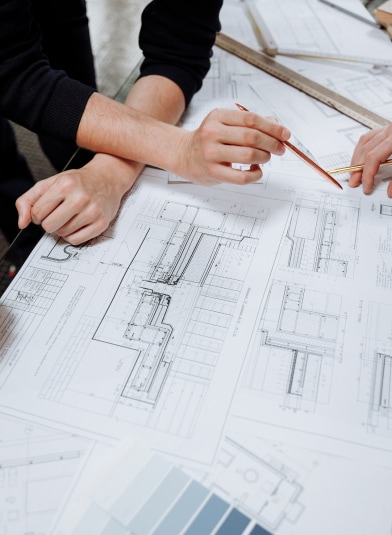
train station renovation (2016-2017)
- Applications of Titanium Bolts, Fasteners, and Washers
Titanium bolts, fasteners, and washers find extensive applications across various industries due to their exceptional properties. The following are some detailed examples of their applications:
Aerospace Industry:
Aircraft Assembly and Components: Titanium bolts and fasteners are widely used in the assembly of aircraft structures, including wings, fuselage, and landing gear. Their high strength, lightweight nature, and corrosion resistance make them suitable for critical connections.
Engine Mounting Systems: Titanium bolts are employed in securing aircraft engine components, withstanding the high temperatures and vibrations associated with engine operations.
Structural Connections: Titanium bolts play a crucial role in joining structural components in aerospace applications, ensuring integrity, strength, and longevity.
Spacecraft and Satellites: Construction of spacecraft and satellites, where lightweight materials are essential to reduce launch costs and improve performance.
Automotive Industry:
High-Performance Racing Vehicles: where weight reduction is critical for enhanced speed and agility.
Suspension Systems: Assembly of suspension systems, providing strength and durability while reducing overall weight.
Exhaust Systems: High-performance exhaust systems, as they can withstand high temperatures and corrosive environments.
Exhaust Systems: Used in high-performance exhaust systems, as they can withstand high temperatures and corrosive environments.
Engine Components: Titanium bolts secure critical engine components, such as cylinder heads, connecting rods, and crankshafts, delivering strength and reliability in demanding automotive applications.
Marine Industry: Shipbuilding and Offshore Structures: Titanium bolts and fasteners are utilized in the construction of ships and offshore structures, where resistance to corrosion in saltwater environments is crucial.
Subsea Equipment: Titanium fasteners are employed in subsea equipment such as pipelines, risers, and underwater installations, offering excellent corrosion resistance and strength.
Propeller Systems: Titanium bolts find application in propeller systems, as they provide a lightweight solution while withstanding the harsh marine environment.
Medical and Dental Applications:
Implants and Prosthetics: Titanium bolts and fasteners are used in medical implants, including orthopedic implants, dental implants, and spinal fixation devices. The biocompatibility, strength, and corrosion resistance of titanium make it an ideal choice for long-term implantation in the human body.
Surgical Instruments: Titanium fasteners are utilized in surgical instruments, as they offer lightweight yet robust solutions that can withstand repeated sterilization processes.
Sports and Recreation:
Bicycle Frames and Components: Titanium bolts and fasteners find use in bicycle frames, forks, and other components. The lightweight nature and strength-to-weight ratio of titanium contribute to improved performance and ride quality.
Racing Yachts: Titanium bolts and fasteners are utilized in the construction of racing yachts, where weight reduction is essential to achieve faster speeds.
- Manufacturing Methods of Titanium Bolts
The production of titanium bolts involves several key manufacturing steps to ensure high-quality and precise components. The manufacturing process typically includes the following stages:
Titanium Bar Stock Preparation:
The manufacturing process begins with the preparation of titanium bar stock. Titanium bars, available in various grades and sizes, are selected based on the specific requirements of the bolts. These bars undergo rigorous quality checks to ensure they meet the desired standards.
Machining Techniques:
Titanium bars are then subjected to machining techniques such as turning, milling, and drilling. These processes involve removing excess material and shaping the titanium into the desired bolt shape. CNC (Computer Numerical Control) machines are commonly used to achieve precise and consistent dimensions.
Machining titanium presents certain challenges due to its high strength and low thermal conductivity. Special attention is given to tool selection, cutting parameters, and coolant usage to optimize the machining process and minimize the risk of heat build-up, tool wear, and surface defects.
Heat Treatment:
After the initial machining process, the titanium bolts may undergo heat treatment to enhance their mechanical properties. Heat treatment can involve processes such as annealing, solution treatment, or age hardening, depending on the specific titanium alloy being used. This step aims to improve the strength, hardness, and overall performance of the bolts.
Surface Finishing:
Surface finishing techniques are employed to enhance the appearance and functionality of the titanium bolts. This may include processes like polishing, buffing, or applying protective coatings. Surface treatments also play a role in improving the corrosion resistance of titanium bolts, ensuring their longevity and performance in various environments.
Quality Control:
Throughout the manufacturing process, rigorous quality control measures are implemented to ensure that the titanium bolts meet the required specifications and standards. This includes dimensional inspections, material testing, and mechanical property assessments. Non-destructive testing methods, such as ultrasonic or X-ray inspections, may also be employed to detect any internal defects.
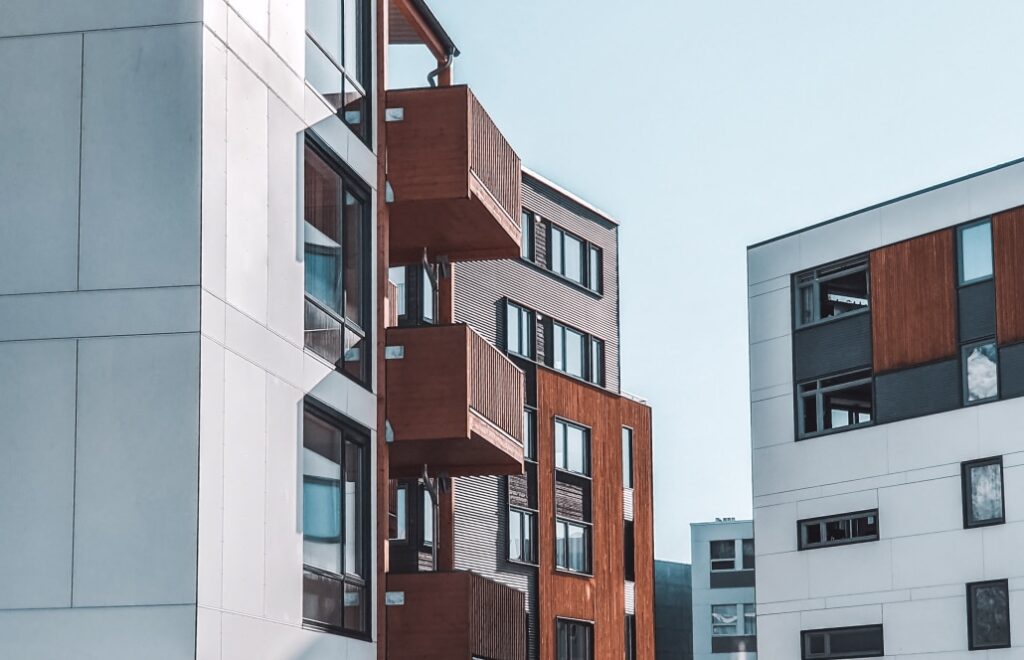
you asked we answer
What is your service area?
How many years of experience do you have?
What services do you offer?
Are you licensed and Insured?
What is the construction process?
What happens if the project goes over budget?
How long does it take to get an estimate?
Will I be able to request changes during the project?
We build partnerships with our clients
Danny freeman
“We have worked with Skybuilders on all of our projects over the past 10 years. They are professional to work with and consistently produce high quality results.”

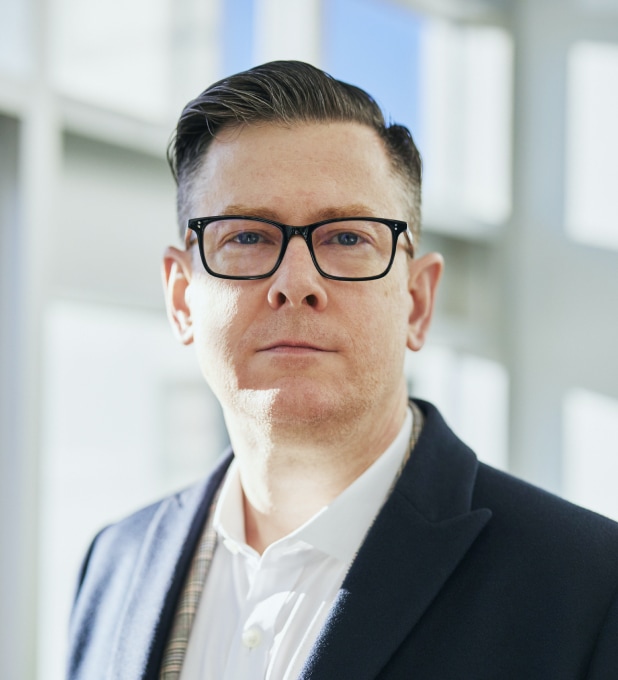
ready to build A future with us?
Lorem ipsum dolor sit amet, consectet adipiscing elit,sed do eiusm por incididunt.
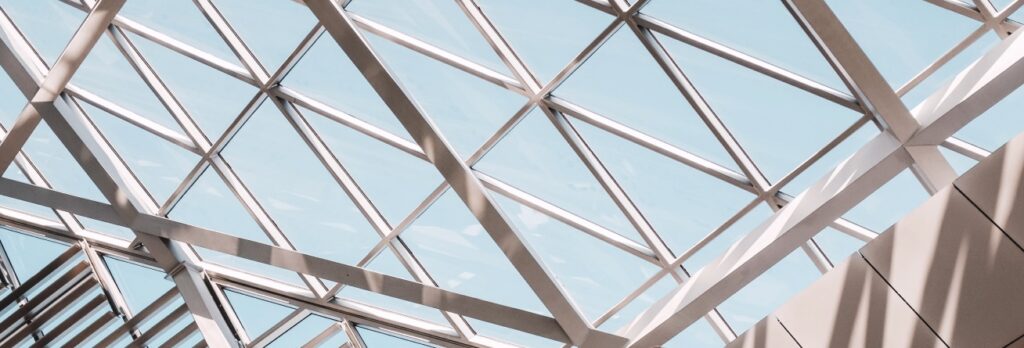