Metal Anodizing Service - Custom Parts
GY Machining’s finishing service to anodize your unique parts.
GY Machining offers the following anodizing colors:
- Gloss, Matte, Texture, Patterns.
- Silver, Red, Purple, Pink, Green, Blue, Brown, Orange, Gold, etc
All uploads are secure and confidential.
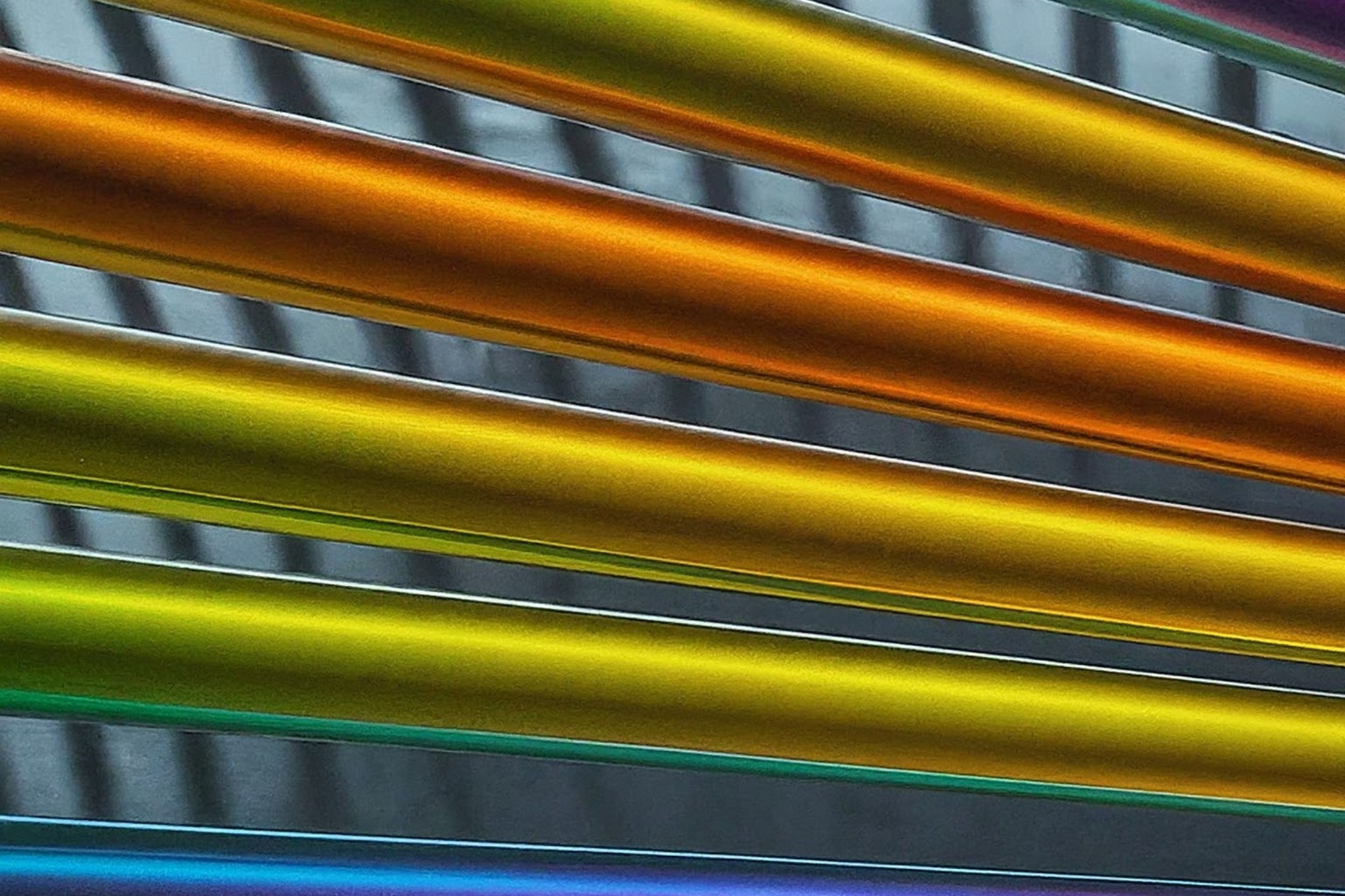
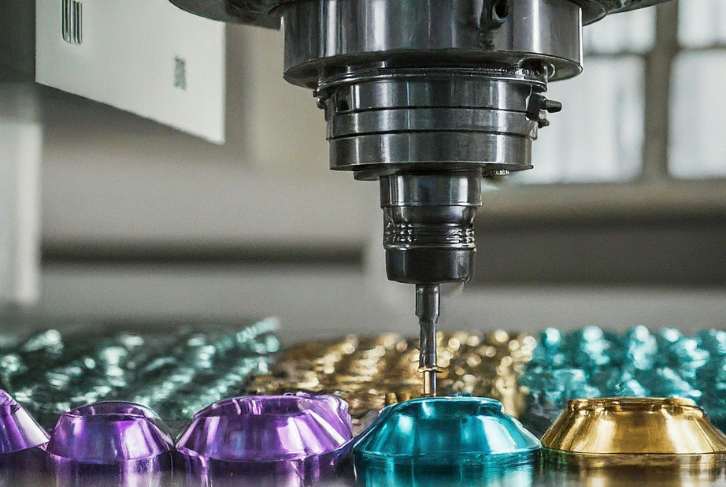
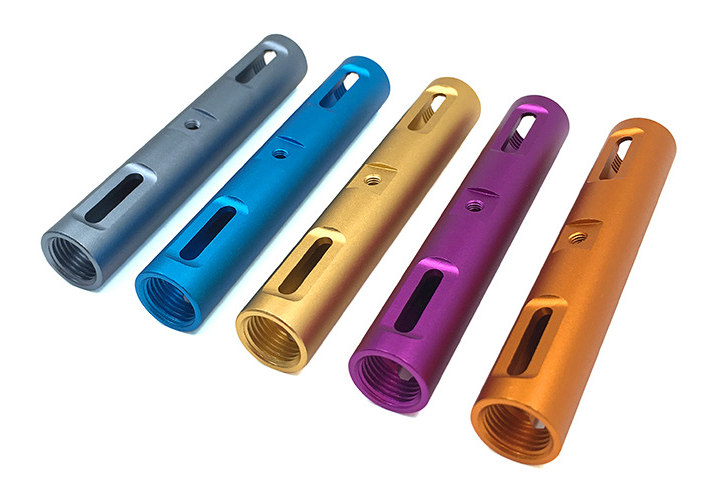
What is Anodizing?
Anodizing is an electrochemical process that significantly enhances the surface properties of metals, particularly aluminum and titanium. It achieves this by thickening the natural oxide layer, creating a highly desirable protective coating. This coating significantly improves the metal’s corrosion resistance, making it ideal for applications that demand extended lifespans in harsh environments.
Key benefits of anodizing include:
- Enhanced Durability: The increased oxide layer provides superior protection against wear and tear, extending the lifespan of metal components.
- Superior Corrosion Resistance: Anodizing creates a robust barrier against corrosion, safeguarding the underlying metal from harmful environmental factors.
- Cost-Effective Choice: Compared to other metal finishing techniques, anodizing offers a balance of effectiveness and affordability.
- Environmentally Friendly: Anodizing typically utilizes processes with minimal environmental impact, reducing concerns about ventilation and disposal.
- Aesthetic Appeal: Anodizing not only protects the metal but can also be used to achieve a variety of attractive finishes, enhancing the visual appeal of the product.
Beyond Aluminum: Versatility of Anodizing
While frequently used for aluminum, anodizing can also be effectively applied to other metals like magnesium, titanium, zinc, and copper. This broad applicability makes anodizing a valuable tool for various industries.
How Anodizing Works?
Anodizing is an electrolytic process that transforms a metal’s surface by creating a robust protective oxide coating. This coating boasts exceptional corrosion resistance and wear resistance, safeguarding the metal from environmental threats and daily wear and tear. Anodizing also offers the remarkable ability to imbue the metal with a spectrum of unique colors, enhancing its visual appeal for various applications.
Unlocking the Science Behind Anodizing
The anodizing process is achieved by strategically submerging the metal in a precisely formulated acidic solution. An electric current is then meticulously passed through the solution and the metal itself. This carefully controlled process triggers the formation of a desirable oxide layer on the metal’s surface.
Precision Control for Optimal Results
The resulting oxide layer’s thickness is meticulously controlled through two key factors:
- Immersion Duration: The length of time the metal is submerged in the acidic solution directly influences the oxide layer’s final thickness.
- Electric Current Strength: The strength of the electric current plays a crucial role in determining the final thickness of the oxide layer.
A Favorable Choice for Diverse Applications
Anodizing has emerged as a highly sought-after process due to several compelling advantages:
- Swift Execution: Anodizing is a relatively quick process, making it an attractive option for high-volume industrial applications.
- No Harmful Chemicals: Unlike some metal finishing techniques, anodizing avoids the use of toxic chemicals, promoting a safer work environment.

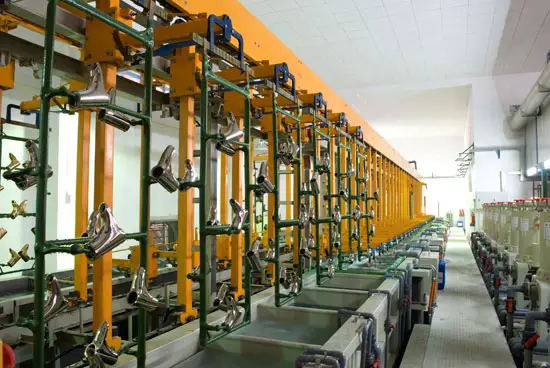
Anodizing Options
Type II Anodizing
Naturally occurring oxide layers on metals are incredibly thin, typically only 2-3 nanometers (billionths of a meter). In contrast, Type II anodizing creates a significantly thicker oxide layer ranging from 1.8 micrometers (µm) to 25 micrometers (µm). To visualize this difference, one micrometer is 1,000 times thicker than a nanometer. (Note: µm is the abbreviation for micrometer).
Uniform and Consistent Coating
When applied correctly, Type II anodizing results in a highly regular and uniform oxide layer across the entire treated surface. This consistency is crucial for achieving a visually pleasing aesthetic finish, particularly for decorative applications.
“Request a Quote for Custom Anodized Parts”
Hardcoat Anodizing (Type III)
While natural oxide layers on metals are mere wisps, typically only 2-3 nanometers thick, Type III anodizing takes things to a whole new level. This advanced process dramatically increases the oxide layer’s thickness, reaching or surpassing an impressive 50 micrometers (µm), which is 0.002 inches! (Remember, a micrometer is 1,000 times thicker than a nanometer.)
Superior Strength, Exceptional Results
The beauty of Type III anodizing goes beyond just impressive numbers. When properly applied, it creates a remarkably uniform and consistent layer across the entire treated surface. This translates to unmatched durability and scratch resistance. Go ahead, try scratching it with a knife – you won’t! (Note: This emphasizes the benefit with a touch of informality.)
Type III Anodizing: Rooted in Military Standards
Similar to Type II, Type III anodizing finds its origins in the rigorous standards of the military (Mil-A-8625 Type III category). This heritage signifies its commitment to delivering exceptional performance and reliability.